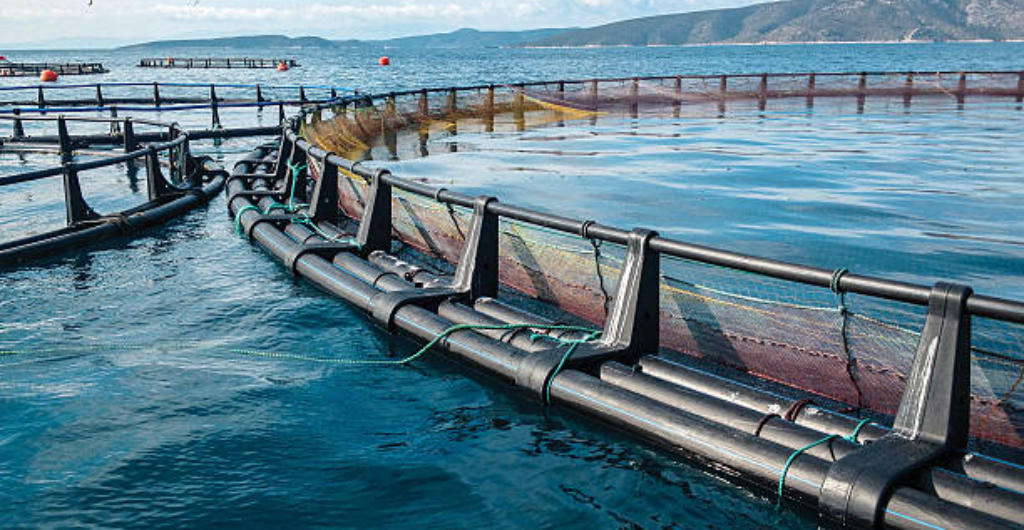
Polyethylene (HDPE) has become the gold standard in piping materials for aquaculture and fish farming. Its chemical resistance, flexibility, and long lifespan make it a perfect fit for marine and freshwater environments. This article explores how HDPE Pipe Systems for Aquaculture support the needs of aquaculture facilities, from tank-based farms to open-sea operations.
As the industry moves toward higher sustainability and operational efficiency, infrastructure choices play a pivotal role. HDPE piping offers not only technical advantages but also economic and environmental benefits, enabling farm operators to reduce water loss, maintain optimal living conditions for aquatic species, and streamline system maintenance. From hatcheries to offshore cages, HDPE adapts to diverse installation scenarios with proven reliability.
Why HDPE is ideal for aquafarming infrastructures
Aquaculture operations face unique environmental and logistical challenges. HDPE addresses these demands by offering reliability and performance across diverse installations. Its resistance to chemical degradation, mechanical impact, and biological growth makes it the preferred choice for underwater pipelines, hatchery water systems, and large-scale fish farming installations.
HDPE’s ability to perform in corrosive and high-moisture environments eliminates many of the failures common with traditional piping. It allows aquaculture engineers to design systems that are both durable and easy to maintain—key features for installations in coastal zones or remote marine facilities.
Moreover, HDPE is lightweight compared to metal alternatives, which simplifies transport and installation, especially in offshore projects where logistics are complex and costly.
Corrosion resistance in seawater environments
Seawater is highly corrosive, especially to metallic components. HDPE is inherently resistant to saltwater corrosion, ensuring pipe longevity without additional protective coatings. This property makes it suitable for submerged networks, hatchery water supplies, and marine recirculation systems.
Unlike metal pipes, which can suffer from corrosion and, HDPE maintains its structural and hydraulic properties even after prolonged exposure to seawater. This extends the service life of the entire system.
Additionally, HDPE resists degradation from UV exposure, marine organisms, and cleaning agents used in aquafarming environments. These attributes help operators maintain system integrity with minimal chemical use, supporting both sustainability and animal welfare standards.
Flexibility for underwater and tank systems
HDPE’s flexibility allows it to absorb wave movement and ground shifting without cracking. For submerged systems, the material resists deformation under water pressure, maintaining consistent water flow and system integrity.
This natural flexibility also minimizes the risk of structural failure caused by seabed movement or vessel activity. It is especially beneficial in floating cage systems or installations located in tidal zones, where movement and vibration are constant.
Furthermore, the ability of HDPE to bend without breaking allows for simplified layouts, reducing the number of fittings required. This not only cuts down on installation time but also lowers the risk of leakage points, creating a more resilient piping network.
PE Piping solutions for sustainable fish farming
Sustainability in aquaculture requires efficient, low-impact systems. HDPE supports this goal through its extended lifecycle and energy-efficient transport characteristics. Its manufacturing and installation processes consume less energy compared to traditional materials, and its smooth internal surface enhances hydraulic performance.
Additionally its long lifespan reduces material waste and limits the frequency of system overhauls.
This material choice helps aquaculture operators meet environmental regulations and certification standards, including those related to emissions, durability, and end-of-life disposal. As sustainability becomes a competitive advantage, HDPE offers both environmental and financial returns.
Marine-Grade HDPE Fittings: features and materials
Marine-grade HDPE fittings are designed for durability and chemical resistance. Plastitalia manufactures these fittings using PE100RC material, optimized for submerged and pressurized environments. These components are certified to international standards, ensuring safe use in food-grade applications.
PE100 fittings provide superior strength-to-weight ratios and retain performance even under extreme environmental loads. Their resistance to UV radiation, microbial attack, and salt crystallization ensures consistent operation in aquaculture conditions.
These fittings are available in a wide range of configurations, including elbows, tees, reducers, and flanges, allowing flexible adaptation to complex marine installations.
Installation techniques in marine and submerged settings
Installing pipe networks in aquaculture demands technical precision and environmental adaptation. HDPE Pipe Systems for Aquaculture offers versatile welding and anchoring options that support long-term use in marine settings. It allows for efficient deployment even in harsh or difficult-to-access locations such as sea pens or deepwater farms.
Plastitalia’s solutions are tailored for offshore conditions and include fittings designed for easy on-site handling and reliable connections—even when operations are limited by tides, waves, or limited technical infrastructure.
Electrofusion and butt welding in aquaculture
Electrofusion and butt fusion welding create seamless, leak-proof joints essential for maintaining water quality and minimizing system failure.
These welding techniques eliminate the need for mechanical joints or gaskets, reducing potential failure points. Once welded, the pipe system behaves as a single, continuous structure with uniform strength and resistance.
Anchoring Systems for underwater pipes
Submerged HDPE Pipe Systems for Aquaculture must be stabilized against currents and seabed movement. Anchoring systems using concrete blocks, HDPE saddles, or ballast couplers are commonly used to secure the pipe without compromising flexibility. These systems help maintain alignment and flow direction across variable depths.
Proper anchoring also prevents uplift or dragging, protecting the network from storm surges and vessel interference. Installation methods can be adjusted to suit different bottom conditions—rocky, sandy, or silty—ensuring secure placement in any marine context.
Long-Term ROI for aquaculture pipe networks
Investing in HDPE Pipe Systems for Aquacultureoffers long-term financial and operational benefits, especially when compared to traditional materials like PVC, fiberglass, or metal. The upfront cost is offset by durability, ease of installation, and virtually maintenance-free performance.
For aquaculture businesses, this translates into reduced downtime, fewer repair interventions, and better system reliability—all crucial for sustaining continuous production cycles.
Lower maintenance vs traditional materials
HDPE requires minimal maintenance over its lifetime. It does not rust, scale, or degrade from UV or salt exposure. This significantly reduces the need for repairs, downtime, and labor interventions. In remote aquaculture operations, this translates to lower operational costs and greater reliability.
Maintenance activities such as flushing, inspection, and component replacement are simplified, allowing staff to focus on production rather than infrastructure issues.
Performance metrics in operational farms
HDPE systems contribute to improved water quality, stable temperatures, and controlled flow—all essential for healthy stock and efficient production. Case studies from operational farms show a reduction in water loss, fewer pipe failures, and greater flexibility in farm design.
With HDPE, farmers can design systems that adapt to changing stocking densities or production goals without compromising system integrity or increasing operational risk.
Conclusion: HDPE Piping as the backbone of modern aquaculture
HDPE pipe systems represent the most advanced and reliable solution for aquaculture and fish farming infrastructures. Their resistance to corrosion, flexibility under dynamic marine conditions, and seamless welding capabilities ensure safe, efficient, and long-lasting operation in both onshore and offshore settings.
As global demand for sustainable seafood production rises, aquaculture businesses must rely on infrastructure that can adapt and perform under pressure. HDPE not only meets these expectations but surpasses traditional materials in terms of durability, environmental performance, and cost efficiency.
Plastitalia stands as a trusted partner in the aquaculture sector, offering marine-grade HDPE fittings, expert consultation, and customised solutions tailored to the unique needs of each installation. Whether you’re expanding a fish hatchery or building a large-scale offshore farm, Plastitalia ensures your piping systems are future-ready, compliant, and built to last.