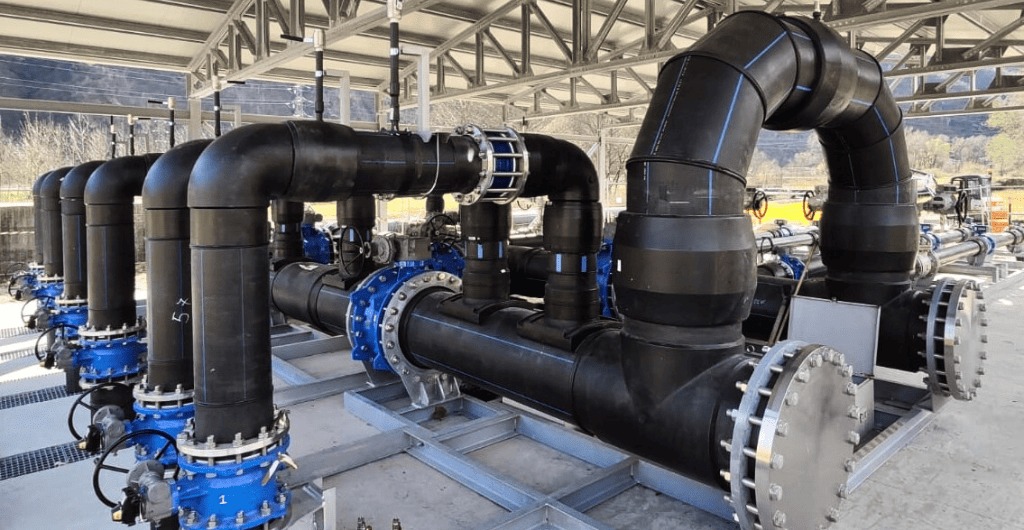
HDPE electrofusion technology has become a cornerstone of modern water infrastructure, offering a dependable method to ensure leak-proof, long-lasting joints in polyethylene piping systems. Designed for durability and safety, these solutions are widely used in municipal, industrial, and civil engineering projects.
This article explores the key benefits of HDPE electrofusion systems, their role in water pipeline applications, best installation practices, and the long-term advantages for public and private water networks.
Why Use HDPE Electrofusion Fittings for Water Pipelines?
Electrofusion fittings represent one of the most efficient and secure methods to join HDPE pipes in modern water supply systems. These fittings are embedded with precisely placed electrical heating elements that, once activated, melt the contact surfaces of both pipe and fitting, resulting in a homogeneous, high-strength weld. The process ensures consistency, safety, and repeatability—key factors in large-scale infrastructure projects.
In addition to performance, HDPE electrofusion offers a clean and compact solution that minimizes installation space and reduces the need for mechanical components such as flanges or bolts. This is especially important in environments where access is limited or where buried pipelines must remain maintenance-free for decades.
Compared to mechanical jointing methods, electrofusion provides a superior level of sealing, making it the preferred technique in systems that demand high integrity, such as potable water networks and critical infrastructure.
Resistance to corrosion, pressure, and environmental stress
HDPE electrofusion fittings offer excellent resistance to corrosion, eliminating the risk of rust or degradation that commonly affects metal fittings in wet or chemically aggressive soils. They maintain full mechanical integrity when exposed to fluctuating temperatures, high humidity, or aggressive chemical agents—including chlorinated water and industrial discharge.
Unlike traditional systems, electrofusion joints are unaffected by microorganism growth, ensuring hygienic transport of potable water and reducing internal contamination risks. This makes them ideal for both urban and rural water systems where water quality must remain constant throughout the network.
From a mechanical perspective, these fittings are engineered to withstand internal pressure surges and external loads. They can absorb dynamic stresses caused by water hammer, soil movement, and traffic loads without cracking or leaking. This performance is essential for long-term reliability in buried installations and aboveground systems alike.
The absence of mechanical fasteners means fewer weak points in the pipeline, translating into greater structural continuity and reduced maintenance over the system’s lifecycle. The result is a robust, low-risk installation that offers peace of mind for municipalities, contractors, and utility operators.
Key products for water infrastructure
Electrofusion technology enables the integration of specialized fittings that address the complex demands of modern water infrastructure. These fittings allow for flexible pipeline configurations, including directional changes, dimensional adjustments, and network expansions—essential for building scalable and high-performing systems.
Each component plays a specific role in ensuring fluid continuity, mechanical strength, and system integrity. Whether for new installations or upgrades to existing water systems, HDPE electrofusion fittings provide precision, reliability, and efficiency across all phases of pipeline design and deployment.
Electrofusion Couplers, Reducers, and Tees
Electrofusion Couplers are fundamental in connecting two pipe ends with maximum sealing strength. Their internal resistance wires ensure uniform heating and bonding across the joint, making them ideal for both high-pressure and buried installations. Available in a wide range of diameters, couplers ensure leak-free connections that comply with international standards.
Electrofusion Reducers are used when transitioning between different pipe sizes within the same system. They maintain consistent hydraulic performance, avoiding turbulence and ensuring a smooth, controlled flow. This is especially valuable in systems that combine various pipe dimensions due to local constraints or hydraulic design requirements.
Electrofusion Tees are critical for creating lateral branches in complex pipeline grids. They enable efficient water distribution without compromising the mechanical strength of the network. Thanks to their geometry and electrofusion process, tees provide high structural integrity even in multidirectional layouts.
All fittings are manufactured from PE100 high-density polyethylene, offering exceptional resistance to internal pressure, environmental stress, and aggressive soil conditions. Their compact form factors allow easier installation in confined areas, while the electrofusion process ensures a permanent and reliable weld.
In water infrastructure projects where durability, precision, and safety are priorities, these fittings represent a key asset. They support both standard and custom configurations, making them suitable for a wide range of municipal and industrial water systems.
Best Practices for installing water pipeline fittings
Proper installation is essential to guarantee the long-term performance and safety of HDPE water pipeline systems. Electrofusion, while highly effective, demands strict compliance with preparation and welding protocols. Every phase of the process—from surface treatment to quality control—must be carried out with precision to achieve optimal results.
Environmental factors such as temperature, humidity, and cleanliness must be monitored closely during installation.
In addition, personnel must be properly trained and certified to carry out HDPE electrofusion welding. Using uncalibrated tools or skipping standard procedures may result in defective joints, potentially affecting the entire pipeline system.
Electrofusion techniques and PN Rating Selection
To create a strong and uniform bond, pipe ends must be thoroughly cleaned of dirt, oxidation, and grease. A scraping tool is used to remove the oxidized surface layer, exposing the virgin material underneath and ensuring full contact with the fitting’s embedded heating wire. Proper alignment is then critical—any angular deviation may lead to weld failure or leakage.
Once the pipe and fitting are aligned, the electrofusion control unit (ECU) applies a specific voltage and current for a predefined time, depending on the fitting’s barcode or manual parameters. This process ensures even heat distribution and forms a homogeneous, high-strength joint.
An equally important consideration is the PN (Nominal Pressure) rating, which defines the pressure capacity of the pipe and fitting assembly. Selecting the right PN class—typically PN10, PN16, or PN25—is based on multiple factors including the fluid being conveyed, pipe diameter, installation depth, and system pressure fluctuations.
Correct PN selection ensures not only regulatory compliance but also protects the system from premature stress, fatigue, or rupture under operating conditions. When properly installed using the right techniques and pressure ratings, HDPE electrofusion fittings deliver decades of leak-free performance in even the most demanding environments.
Long-Term benefits for municipal and industrial water systems
Investing in HDPE electrofusion solutions is not only a matter of immediate performance but also a strategic decision that ensures long-term system integrity. Municipalities and industrial operators increasingly rely on HDPE for water infrastructure due to its ability to maintain reliability over decades, even under variable and demanding operating conditions.
Beyond the technical benefits, the use of HDPE electrofusion fittings supports sustainability objectives. These systems contribute to reduced water loss, lower energy consumption, and more efficient resource management—key priorities for modern utilities and environmental regulators alike.
For infrastructure contractors and engineering firms, HDPE solutions simplify lifecycle planning, minimize risk exposure, and increase the predictability of operational costs over time.
Durability, Safety, and Low Maintenance Costs
The exceptional mechanical and chemical resistance of HDPE ensures that fittings can endure internal pressure, external loads, and chemical exposure without degrading. The electrofusion welding process creates fully sealed joints that are immune to infiltration or exfiltration, unlike gasketed or flanged systems that may loosen over time.
This permanent joint integrity translates to enhanced system safety, particularly in water supply lines where contamination control is critical. HDPE’s smooth internal surface also minimizes biofilm accumulation and helps preserve water quality throughout the distribution system.
From a maintenance perspective, HDPE systems require fewer interventions, significantly lowering the need for periodic inspections, part replacements, or emergency repairs.
Over time, the reduction in unplanned service disruptions, repair crew deployments, and water loss directly impacts the bottom line. For municipalities managing aging infrastructure or industries seeking high-availability utilities, HDPE electrofusion offers a scalable, cost-efficient solution built to last.
Conclusion: optimizing water networks with HDPE Electrofusion Solutions
As water infrastructure faces increasing demands for efficiency, longevity, and safety, HDPE electrofusion fittings offer a proven solution that meets and exceeds modern engineering standards. From rural pipelines to urban water systems, their versatility and performance continue to drive adoption worldwide.
Plastitalia’s extensive range of certified HDPE electrofusion fittings is engineered for the highest standards of reliability in water distribution projects. With decades of expertise and a global reach, the company supports B2B partners with advanced products, technical guidance, and scalable solutions for water pipeline systems.