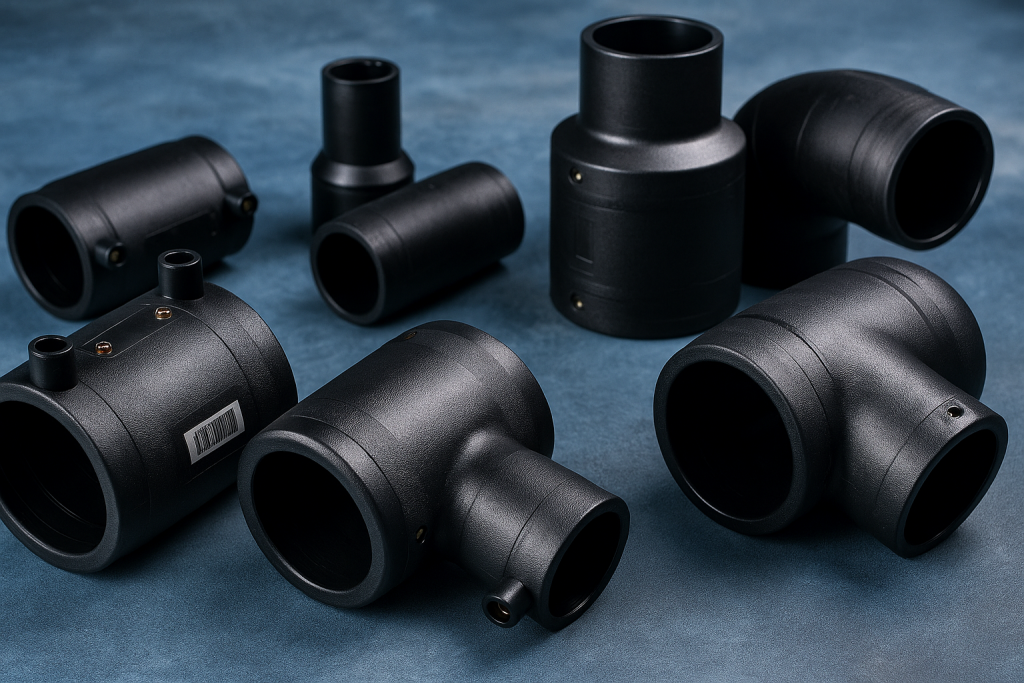
Polyethylene electrofusion fittings play a vital role in the construction of modern pipeline systems. Known for their reliability and performance, these fittings provide a seamless solution for joining HDPE pipes in sectors where safety, durability, and compliance are non-negotiable. Whether used in gas distribution, potable water networks, or industrial infrastructure, their benefits go far beyond conventional connection methods.
In this article, you will learn how polyethylene electrofusion fittings enhance pipeline safety and help meet international standards. We’ll also explore common installation pitfalls, operator certification, and essential technical insights to help procurement and engineering teams make informed decisions.
How Electrofusion enhances pipeline safety
Polyethylene electrofusion fittings have revolutionized pipeline connections by offering a reliable, high-performance method of welding HDPE pipes. These fittings ensure a homogenous joint that maintains strength and integrity even under extreme conditions. Their use is essential in sensitive applications like municipal gas supply, potable water distribution, and industrial fluid networks.
Unlike traditional mechanical couplings, electrofusion minimizes the risk of human error and ensures a fully integrated system. This method not only extends the service life of the pipeline but also simplifies compliance with regulatory standards in critical infrastructure projects.
Gas containment and leak prevention
Polyethylene electrofusion fittings have revolutionized pipeline connections by offering a reliable, high-performance method of welding HDPE pipes. These fittings ensure a homogenous joint that maintains strength and integrity even under extreme conditions. Their use is essential in sensitive applications like municipal gas supply, potable water distribution, and industrial fluid networks.
Unlike traditional mechanical couplings, electrofusion minimizes the risk of human error and ensures a fully integrated system. This method not only extends the service life of the pipeline but also simplifies compliance with regulatory standards in critical infrastructure projects.
Mechanical integrity of welded joints
The electrofusion welding process guarantees strong mechanical bonds between pipes and fittings. Once the welding cycle is complete, the joint becomes as strong as the pipe itself, with no need for additional clamps or fasteners.
This mechanical integrity is particularly valuable in high-pressure systems or areas subject to ground movement. The flexibility of polyethylene, combined with the solid connection formed by electrofusion, results in a durable and vibration-resistant network, reducing the likelihood of failures.
Additionally, electrofusion joints provide excellent resistance to fatigue caused by pressure cycling, which is common in municipal and industrial applications. This ensures stable performance over decades, even in fluctuating operational environments.
Safety compliance in water and gas infrastructure
Adhering to international safety standards is a mandatory requirement in regulated industries. Electrofusion fittings are designed and manufactured to meet the strict criteria outlined by global standards organizations.
These standards not only define product quality but also ensure operational safety across the entire infrastructure lifecycle. Companies that adopt certified polyethylene electrofusion fittings can confidently meet legal obligations, lower risk exposure, and enhance project credibility during audits and inspections. This is especially relevant in public sector projects, where compliance is routinely scrutinized by regulatory authorities and third-party evaluators.
Meeting ISO and EN certification requirements
Top-tier polyethylene electrofusion fittings comply with ISO 4427, ISO 4437, EN 12201, and EN 1555 standards. These certifications ensure the product’s suitability for potable water and gas applications, including resistance to environmental stress, pressure fluctuations, and temperature extremes.
In addition to product performance, certified fittings also demonstrate that the manufacturing process itself follows strict quality control protocols. For contractors and utilities, this translates into fewer installation errors, higher system uptime, and reduced liabilities over the long term. Furthermore, certified products support international interoperability—critical for companies working on cross-border infrastructure or complying with multi-national specifications.
Electrofusion traceability and barcode systems
Modern electrofusion fittings incorporate traceability systems through barcodes or RFID tags. These allow operators to scan the fitting and automatically upload the correct welding parameters to the electrofusion control unit.
Traceability is crucial not only during installation but also for long-term maintenance and asset management. By accessing batch history, project managers can quickly identify and isolate potential defects, plan replacements, or coordinate repairs in a timely manner.
This makes polyethylene electrofusion fittings an ideal choice for smart infrastructure systems. Additionally, traceability ensures accountability throughout the supply chain, helping to combat counterfeit components and support regulatory reporting.
Common installation errors and how to avoid them
Despite their reliability, polyethylene electrofusion fittings must be installed correctly to achieve their full performance potential. Improper handling or welding can compromise safety and durability.
For mission-critical applications—such as municipal gas or water networks—installation errors may lead to regulatory non-compliance, costly rework, or even service disruptions. Awareness of common pitfalls is essential for any engineering or maintenance team. Establishing a standardized installation protocol, along with periodic refresher training for field personnel, is a valuable investment in long-term system integrity.
Improper surface scraping and alignment
One of the most common errors during installation is inadequate surface preparation. Before welding, the outer layer of the pipe must be scraped to remove oxidation and contamination. Failure to do so prevents proper fusion and may lead to weak joints or leaks.
Even slight misalignment can affect the integrity of the weld. Inconsistent fusion zones can become future failure points, especially in high-pressure or high-cycle environments. Using calibrated scraping tools and dedicated alignment fixtures is essential to preserve mechanical strength. Additionally, keeping surfaces clean and dry—free from dust, oils, or moisture—helps ensure full material bonding and minimizes the risk of incomplete welds.
Ignoring cooling times and pressure testing
Another frequent mistake is rushing the cooling phase. After welding, joints need time to solidify without movement or stress. Interrupting this process can introduce microcracks or distortions.
Cooling time depends on ambient temperature, pipe size, and weld duration, so following manufacturer specifications is critical. Once cooled, pressure testing must be conducted in accordance with national regulations or project-specific protocols. It is the final checkpoint that validates joint performance before commissioning. Documentation of these tests also plays a crucial role in project traceability, warranty enforcement, and future maintenance planning.
Training and certification for electrofusion operators
Even the best polyethylene electrofusion fittings cannot compensate for poorly trained technicians. Proper installation relies on skilled personnel who understand both the equipment and the materials.
Investing in operator training is not only a matter of compliance—it directly impacts operational efficiency, safety outcomes, and the reputation of the project delivery team. Certified technicians become an asset, capable of preventing costly mistakes in the field.
Importance of qualified installers
Only trained and certified installers should be allowed to handle electrofusion welding in critical infrastructure projects. Certification programs typically include both theoretical modules and hands-on practical assessments to ensure full understanding of electrofusion procedures.
Certified professionals are also better equipped to troubleshoot on-site, adjust to unforeseen conditions, and ensure that each weld meets the highest quality standards. Their presence can streamline inspections and boost client confidence.
Equipment calibration and monitoring tools
Installation success also depends on the performance of the electrofusion control unit. Regular calibration of welding machines ensures consistent energy output and accurate execution of welding parameters.
Using up-to-date monitoring tools also helps document compliance. Weld loggers, barcode scanners, and cloud dashboards create a digital trail of every installation. This transparency is particularly valuable in large-scale infrastructure projects, where traceability and accountability are non-negotiable.
Conclusion
Polyethylene electrofusion fittings offer a reliable, safe, and cost-effective solution for building and maintaining modern pipeline infrastructure. Their ability to deliver high-performance joints with minimal maintenance makes them a preferred choice in water, gas, and industrial systems.
However, the effectiveness of these fittings depends not only on the product itself but also on correct installation, compliance with international standards, and the expertise of trained professionals. From material traceability to operator certification, every step of the process contributes to the long-term integrity of the network.
For procurement teams and project engineers, choosing certified fittings from trusted suppliers—along with proper training and installation protocols—ensures that pipeline systems remain safe, durable, and efficient for decades to come.